Substantial use of alcohol-based hand sanitizer on hands in recent months has become more counterproductive with manufacturers adding just about anything to make it to the top shelves. Little do we know the harmful additions to alcohol which reach our hands over and over.
WHO recommends the use of hand sanitizers with at least 60% Ethanol or Isopropanol for an effective germ kill. But is the one on your hands having the right additive mix?
The demand for hand sanitizers has grown up by a healthy 85% in India today if compared to December 2019 with almost three-fifth demand fulfilled. Since the manufacturing process is rather simple, we saw the emergence of mushroom companies which may get the 60% alcohol content hand sanitizer right, but not the other 40%.
The ‘No’ that need to be addressed:
- Wood alcohol or Methanol is toxic when absorbed through skin. It usually smells bad, dur to addition of methanol, acetonic or other harmful chemicals
- Denatured Alcohol, as they contain benzene a known human carcinogen and should not be consumed or even handled with bare hands
- Addition of antimicrobial Quaternary Ammonium Compounds like Benzalkonium Chloride to reduce the actual alcohol content, minimizing product cost are inadequate against pathogens
- For thicker and luxuriant formulation, manufacturers use carbomers or acrylates which reduce the alcohol efficacy is essentially liquid plastic
- Addition of thickening agents such as glycerin are known to lower the potential of ethanol
- Colourful hand sanitizers are nice to see but are all the colours used even permissible or not. All that glitters is not gold!
The Gel Vs. Liquid Race
Gel based sanitizers are viscous and do not flow easily. Moreover, it takes near about 30 – 40 seconds to act against germs present on our hands. With the average being 0.125 – 0.45 microns big, can easily live between our microscopic skin cracks, whereas the smallest gel-based particle is of 3.5 microns, and ergo the gel cannot reach.
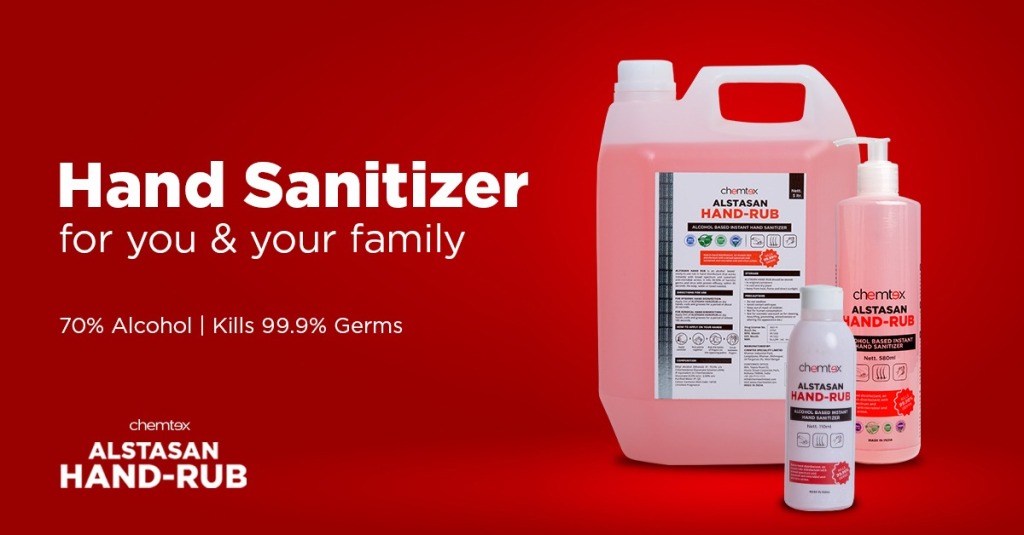
Chemtex Alstasan Hand Rub – Clinical Grade Alcohol based Hand Sanitizer
Chemtex hand sanitizer ingredients include 70% IP grade Ethanol, and 2.5% Chlorhexidine Gluconate, with permissible emollients and moisturizers in purified water. With a refreshing lemon fragrance, it comes in an easy and convenient packaging. The product is licensed under Drug Controller General of India and comes from the house of Chemtex.
Buy Original. Buy Online.